Firestopping Pipe Penetrations
Materials, Issues & Recommendations
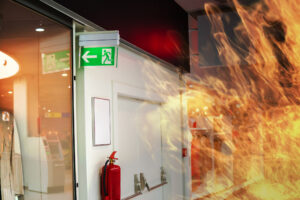
Introduction
Passive fire and smoke barriers in walls, ceilings, and floors are integral to building safety, slowing the spread of fire and smoke. Engineers and architects design mechanical systems using various piping materials for applications such as drain, waste, and vent; water distribution; fire-suppression sprinklers; and other applications. When pipes pass through walls, ceilings, and floors, it is essential to ensure the integrity of fire barriers by using appropriately rated firestop assemblies. If a pipe or other penetration fails due to excessive heat associated with fire and the associated firestop assembly does not remain secured, the resulting gap will compromise the barrier.
“When a fire is actively burning, it’s going to create a lot of heat and pressure,” explains Bruce Johnson, a fire marshal who works with Underwriters Laboratories. “Even the smallest void that’s not protected with proper firestopping almost acts like a blowtorch. You’re going to have really hot flames, gas, and smoke going through that opening… so it rapidly spreads the fire and smoke.”
Failures of firestops and fire barriers can cause devastating tragedies. A fire at the MGM Grand in Las Vegas killed 85 people and injured another 679 when a wall of flames “fed by wallpaper, PVC piping, glue, and plastic mirrors… blew out the main entrance,” according to accounts. “It took six minutes for the entire casino floor to be fully engulfed.”
To protect the lives of building occupants – and first responders – architects, engineers, and construction professionals must ensure these critical components meet the highest standards for safety. Failures in the event of a fire will trigger serious questions – and liability. To that end, this report reviews issues related to firestopping assemblies for various plastic piping materials including polyvinyl chloride (PVC), chlorinated polyvinyl chloride (CPVC), polyethylene (PE), and crosslinked polyethylene (PEX) plastic, as well as non-combustible piping materials such as copper, iron, and steel.
How Pipe Combustibility Affects Firestopping
According to Firefighter Insider, structural fires routinely reach 1,500 degrees Fahrenheit. Plastic pipes start to melt around 413 degrees and begin to combust at about 790 degrees. By contrast, non-combustible copper and iron pipes will not burn; they begin to melt when they reach temperatures of around 2,000 degrees. (Note that steel used in structural beams may lose a significant portion of its strength when the metal reaches a temperature of about 1,100 degrees.) The chart above shows melting and combustion temperatures for commonly used plumbing materials.
Why Firestopping Pipe Can Cause Issues
Despite the combustibility of plastic, many building codes allow use of plastic in plumbing systems, even in buildings with firewalls. This use is permitted with one stipulation, however, and it’s one that turns out to be significant:
Every firestop assembly in a building must meet all applicable regulations.
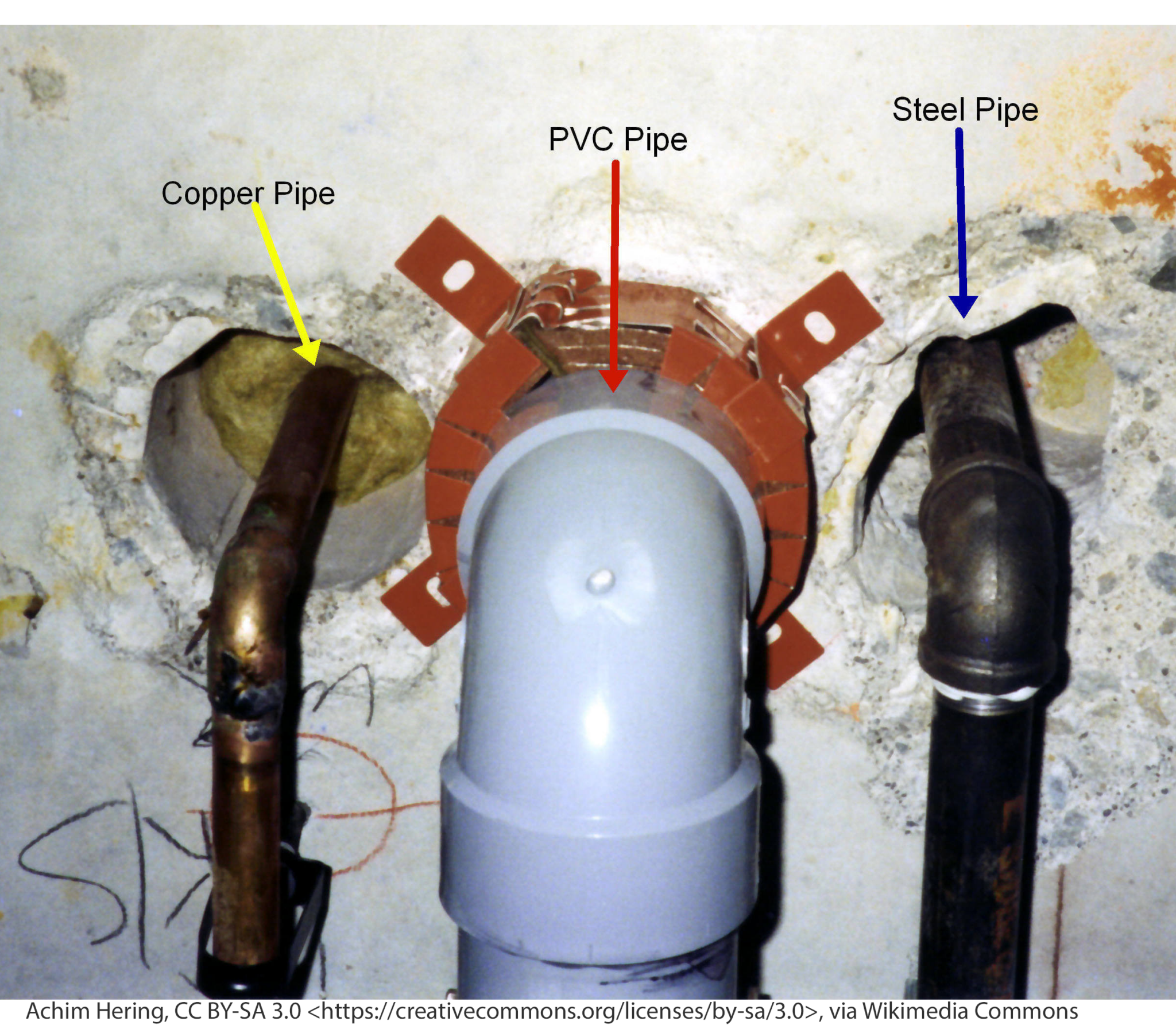
Designing and installing firestop assemblies for piping penetrations requires a demanding process. Teams must understand which code requirements apply to their situation, select appropriate components, and install them correctly.
There are hundreds of different firestop products on the market, and thousands of different firestop configurations, because what’s needed to ensure safety depends on many factors.
Here are a few, but others may apply as well:
- Type of wall, ceiling, or floor material,
- Thickness of the wall/ceiling/floor,
- Location and orientation in the building,
- Pipe diameter, and
- Type of piping material
The consideration of material listed above is particularly important for all plastic pipes for two reasons.
First, various types of plastic – including CPVC, PVC, PEX, PE, and others – are susceptible to chemical damage. According to the Plastic Pipe Institute’s firestopping guide, “firestop sealants may contain chemical additives that can cause damage to plastic pipe.” This means that if a material not compatible with the pipe is used, a chemical interaction could weaken the pipe or cause it to prematurely fail even during normal use.
Second and equally important is the fact that firestop assemblies for plastic pipes are more complicated than firestops for non-combustible metal pipes. Because plastic pipes melt and burn, the assembly must not only account for space around the pipe, but for the space occupied by the pipe itself. A firestop assembly for non-combustible copper and iron pipes may only require these two components:
- Fire-resistant material filling the annular space (typically mineral wool) and
- Firestopping caulk applied around the pipe.
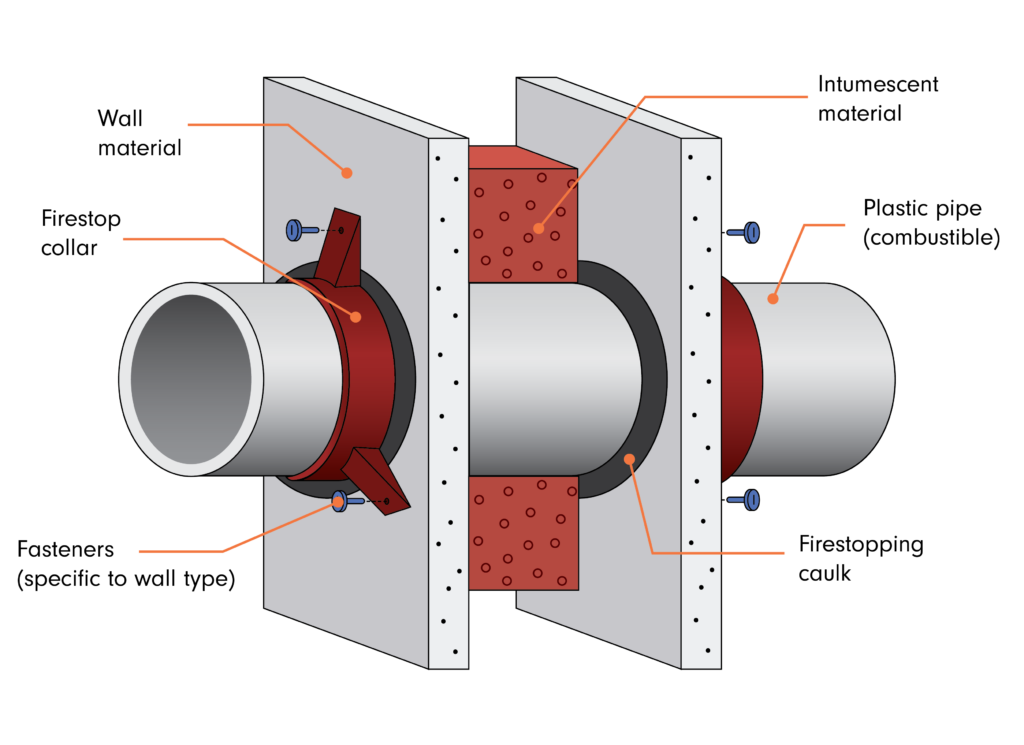
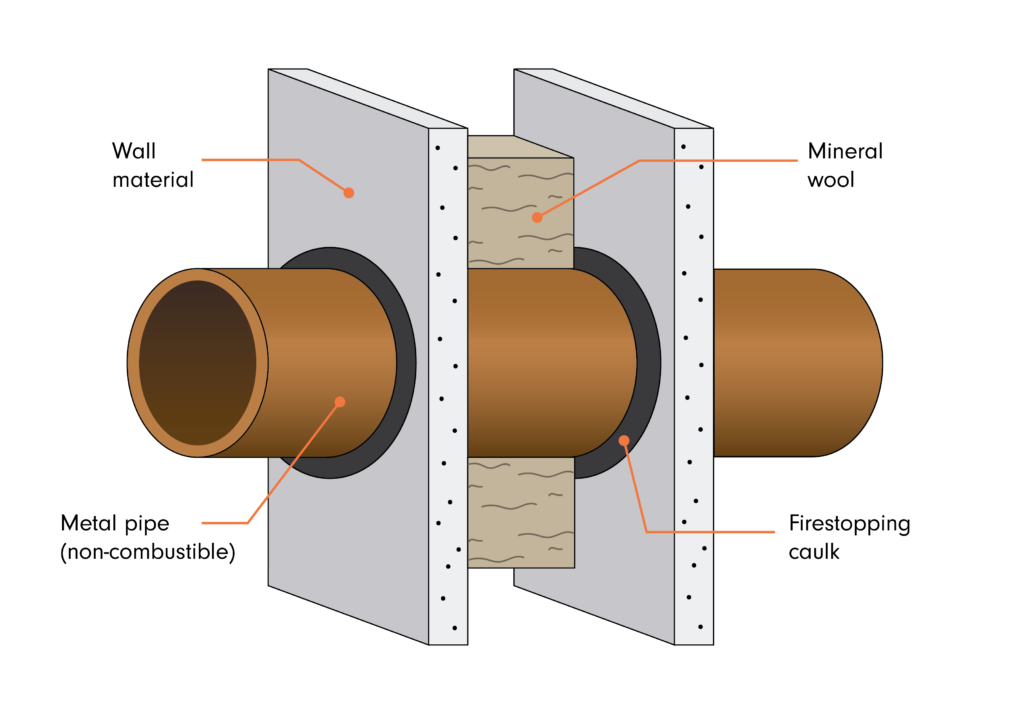
By contrast, assemblies for combustible plastic pipes may feature all the following:
- Intumescent material in the annular space adequate to crush the pipe and fill the entire opening when heated,
- A collar or other device to secure the assembly to the wall, containing the intumescent material in the annular space,
- Fasteners appropriate for the wall type to ensure the collar remains fixed to the wall, and
- Caulk applied around the opening.
As the number of components and combinations in a firestop assembly increases, so does the risk of error. And in practice, firestop experts see more problems in the field with complex assemblies. Firestopping consultant Sharron Halpert dedicates an entire section of her excellent website to identifying “classic mistakes” she’s found in the field, including one installation she says is “very rarely done correctly.”
Common Errors to Avoid
Eirene Knott, Director of Code Services for BRR Architecture, gave Building Safety Journal a good summary of the challenge: “The importance of firestopping in life safety has been well documented but, unfortunately, not well understood,” she wrote. “…Unless you install firestop systems exactly as their listing details, there can be no guarantee that they will perform as intended.” Knott finds that issues occur throughout the building process, a view shared by many other experts in the area. Sources across the industry – including many manufacturers’ websites – offer case studies and other examples.
Here are several issues related to pipe penetrations that can cause failures when inspected:
- Contractors who “roll their own” firestop assembly instead of using a listed system. Most codes require that a listed system be used.
- Contractors who install listed systems for firestop but modify the assemblies and/or fail to follow ALL installation requirements.
- Using firestop systems improperly sized for the annular space they need to protect. “If it’s too small you can’t get sealant placed properly, if it’s too big it can’t survive the hose stream test,” explains Halpert. “If you want to do ONE thing to improve firestop installations (ergo the level of life safety in a building)… it would be to coordinate annular spaces…especially in plastic pipe applications.”
- Mixing products from different manufacturers in the same opening
- Using firestop materials (e.g., caulk) that are not chemically compatible with a given pipe material. This is most common with pipe made of CPVC, HDPE, PEX, and PVC.
- Installing “expired” firestop materials that are beyond the limits of their shelf life. A related problem: installing firestop materials that have been stored or installed at a temperature or humidity that is outside the allowable range. Note that some manufacturers say expired materials are okay to use, so long as they can be troweled into place.
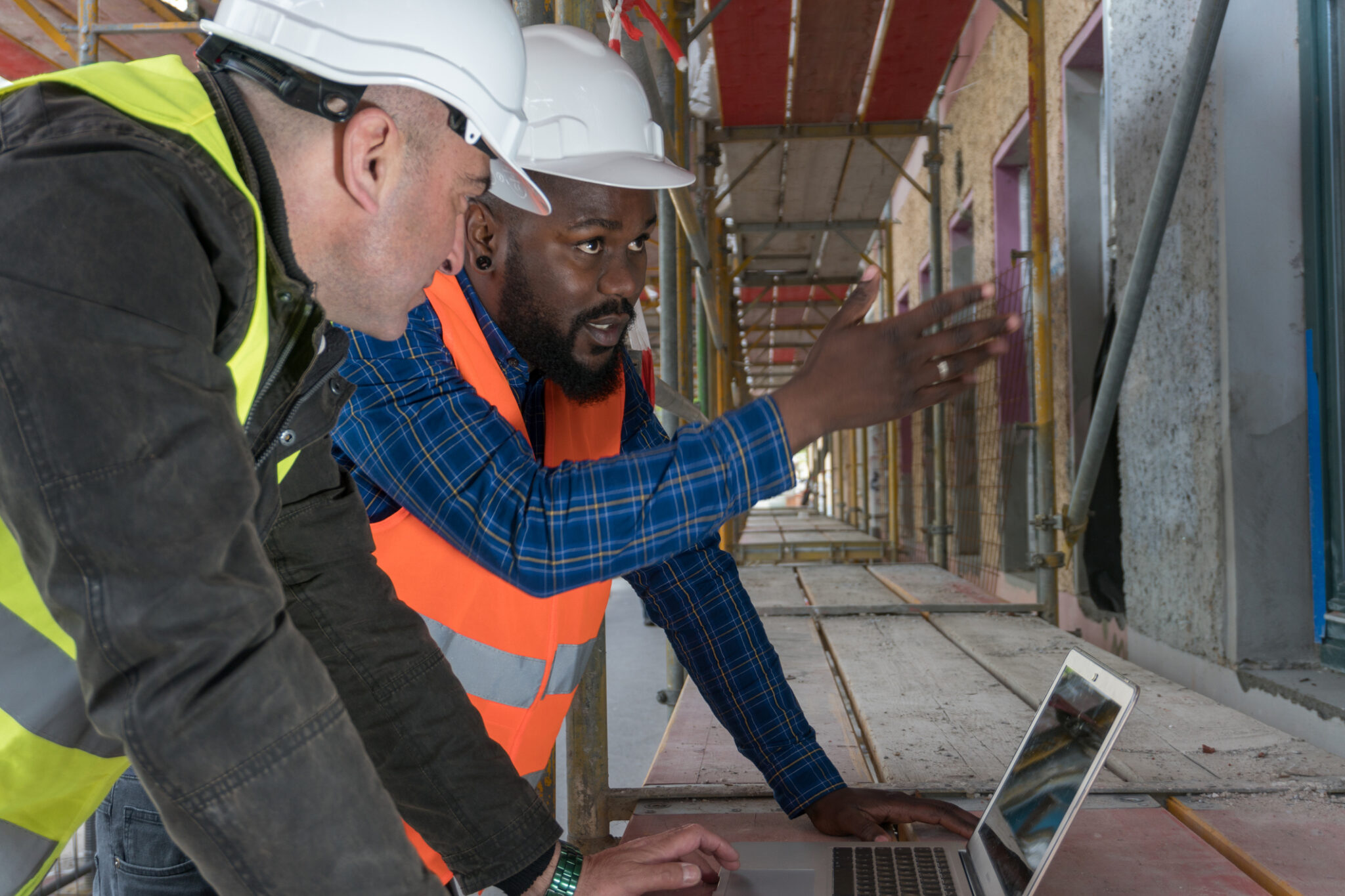
Recommendations
Here are several processes that design and building teams should incorporate into their projects to ensure successful completion of firestopping requirements for piping penetrations:
- Meet with a firestopping consultant at the specification and construction drawing stage to select products that meet all safety requirements. “Plan your firestop BEFORE you make holes,” says Halpert.
- Have the team evaluate which combinations of pipe materials and firestop assemblies will perform best over the life of the building, considering issues such as
- Chemical compatibility between pipe materials and firestopping materials,
- Thermal expansion/contraction of long vertical and horizontal pipe runs, and
- Ease of maintaining and repairing piping systems.
- Consider retaining a single-source firestopping contractor who holds UL certification or has met the requirements for FM4991 – Standard for the Approval of Firestop Contractors accreditation program. “Single source fire stopping is so important because you have one source – meaning one contractor – who is trained and has the knowledge to apply the firestopping,” says fire service lieutenant Rick Conti.
- Commission a special inspection of firestopping, in which the inspector will either witness installation of 10% of all firestop systems or perform destructive testing of 2% of systems. This is required by the International Building Code (IBC) for buildings 75 feet and above by ASTM E2174-14b – Standard Practice for On-Site Inspection of Installed Firestop Systems. If the inspector performs destructive testing, they will be looking to ensure that the installed system meets the requirements and parameters of the specific listed system used in that project.
- Label each listed system used for firestop with the details of the listed system, including
- Manufacturer and model
- Installer name and company, and
- Installation date.
Failing to follow good practices, or installing firestop assemblies incorrectly will put occupants and first responders at risk if a fire occurs. Not to mention exposing architects, engineers, contractors, and owners to significant liability. In a follow-up to her first article, firestopping expert Knott said this about the challenges associated with doing firestopping well: “Clearly, there is quite a lengthy list of items which can result in problems with the installation of firestopping materials… [and] any one of these items can contribute to a two-hour wall being reduced to a four-minute wall.”
To build resilient, safe buildings, design and construction professionals must work to reduce fire risks, and the KISS principle – keep it simple stupid – might be the best way to prioritize safety.